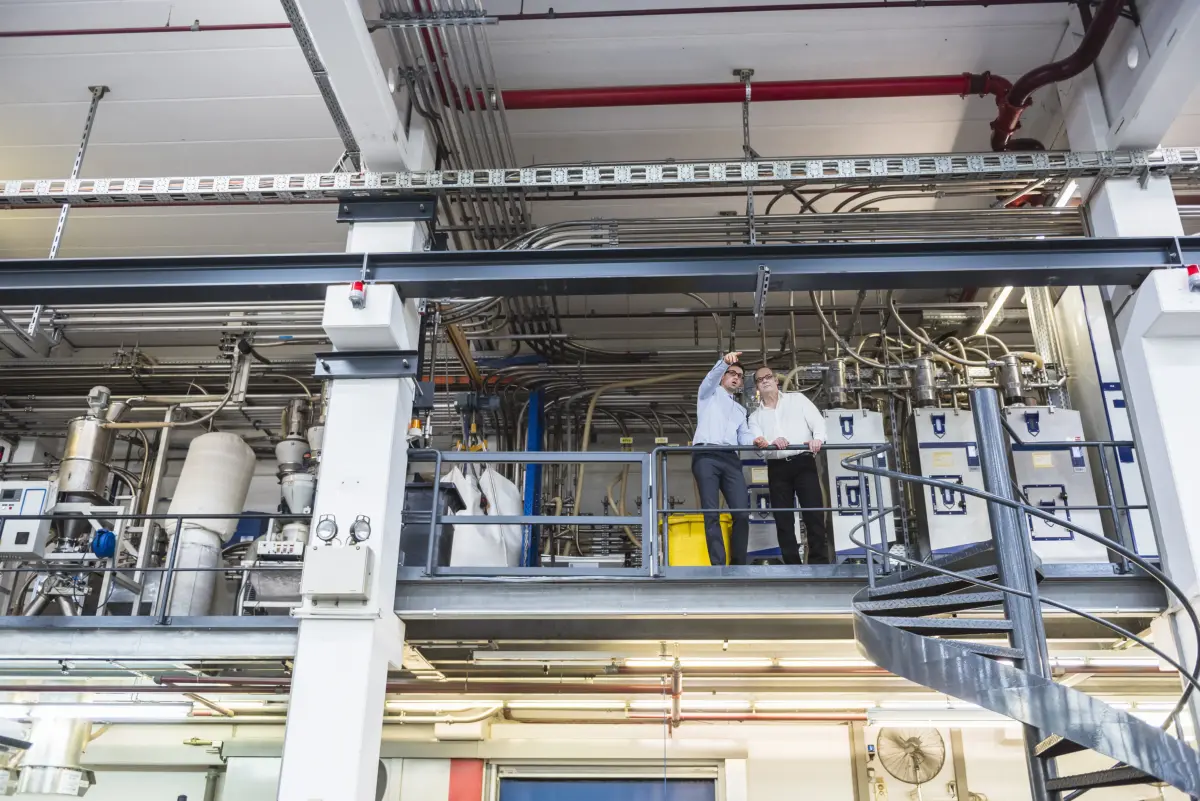
Przemysł produkcyjny przechodzi obecnie bezprecedensową transformację napędzaną przez zaawansowane technologie automatyzacji i robotyzacji. Inteligentne maszyny, systemy AI i rozwiązania Przemysłu 4.0 rewolucjonizują sposób, w jaki fabryki funkcjonują, zwiększając wydajność, obniżając koszty i umożliwiając produkcję spersonalizowanych produktów na masową skalę. W 2025 roku obserwujemy dynamiczny rozwój pięciu kluczowych trendów, które kształtują przyszłość robotyzacji przemysłowej i zmieniają oblicze globalnej produkcji.
Robotyzacja przemysłu to już nie przyszłość, a teraźniejszość. Nowoczesne fabryki coraz częściej stawiają na inteligentne rozwiązania, które nie tylko usprawniają procesy produkcyjne, ale także zwiększają bezpieczeństwo pracowników i poprawiają jakość wytwarzanych produktów. Według najnowszych danych, globalny rynek robotyki przemysłowej osiągnął w 2024 roku wartość 38,09 miliarda dolarów i przewiduje się, że do 2034 roku wzrośnie do 84,36 miliarda dolarów, przy rocznym tempie wzrostu wynoszącym 13,8%.
Robotyzacja produkcji polega na zastępowaniu pracy ludzkiej maszynami i systemami sterowanymi komputerowo. Obejmuje ona różne etapy procesu produkcyjnego, takie jak obróbka materiałów, montaż, kontrola jakości, pakowanie czy transport wewnętrzny. Zautomatyzowane linie produkcyjne są projektowane tak, aby zapewnić optymalny czas wytworzenia produktu i zminimalizować ryzyko błędów.
Warto zauważyć, że nowoczesne rozwiązania w zakresie robotyzacji są dostępne dla firm różnej wielkości. Jeśli chcesz dowiedzieć się więcej o możliwościach wdrożenia takich systemów w swojej firmie, odwiedź stronę elplc.com, gdzie znajdziesz szczegółowe informacje na temat dostępnych rozwiązań i korzyści płynących z automatyzacji procesów produkcyjnych.
1. Sztuczna inteligencja i uczenie maszynowe w robotyce przemysłowej
Integracja sztucznej inteligencji (AI) i uczenia maszynowego (ML) z systemami robotycznymi stanowi jeden z najważniejszych trendów w robotyzacji przemysłu. W 2025 roku roboty wyposażone w AI są zdolne do zaawansowanej interpretacji danych, podejmowania decyzji w czasie rzeczywistym oraz przewidywania potrzeb konserwacyjnych. Dzięki algorytmom uczenia maszynowego, roboty mogą samodzielnie doskonalić swoje umiejętności, adaptować się do zmiennych warunków pracy i optymalizować procesy produkcyjne bez konieczności ciągłego przeprogramowywania.
Kluczowe osiągnięcia w dziedzinie AI i robotyki obejmują zwiększoną autonomię, dzięki której roboty mogą wykonywać złożone zadania, takie jak zaawansowane planowanie, rozpoznawanie wzorców i przewidywanie usterek. Adaptacja w czasie rzeczywistym umożliwia robotom dynamiczne reagowanie na zmiany w środowisku pracy, co znacząco zwiększa ich funkcjonalność i elastyczność. Ponadto, ulepszona łączność między człowiekiem a robotem ewoluuje dzięki specjalistycznej sztucznej inteligencji, która ułatwia płynną komunikację i wykonywanie zadań.
Zastosowania AI w robotyce przemysłowej
Sztuczna inteligencja znajduje zastosowanie w różnych obszarach robotyki przemysłowej. Jednym z najważniejszych jest predykcyjne utrzymanie ruchu, które wykorzystuje algorytmy uczenia maszynowego do analizy danych z czujników i przewidywania potencjalnych awarii sprzętu. Według badań, do 2025 roku aż 66% firm produkcyjnych planuje wykorzystywać predykcyjne utrzymanie ruchu, co stanowi znaczący wzrost w porównaniu do 28% w 2020 roku.
Innym istotnym zastosowaniem AI w robotyce jest optymalizacja procesów produkcyjnych. Algorytmy uczenia maszynowego analizują dane z produkcji i identyfikują obszary, w których można zwiększyć wydajność, zmniejszyć zużycie energii lub poprawić jakość produktów. Ponadto, roboty wyposażone w systemy wizyjne wspierane przez AI mogą przeprowadzać zaawansowaną kontrolę jakości, wykrywając nawet najmniejsze defekty, które mogłyby umknąć ludzkiemu oku.
Zastosowanie AI | Korzyści | Przykłady implementacji |
Predykcyjne utrzymanie ruchu | Redukcja nieplanowanych przestojów, obniżenie kosztów konserwacji | Analiza danych z czujników, wykrywanie anomalii, prognozowanie awarii |
Optymalizacja procesów | Zwiększenie wydajności, redukcja zużycia energii | Analiza danych produkcyjnych, identyfikacja wąskich gardeł |
Kontrola jakości | Poprawa jakości produktów, redukcja odpadów | Systemy wizyjne, wykrywanie defektów |
2. Roboty kolaboracyjne (coboty) – nowa era współpracy człowieka z maszyną
Roboty kolaboracyjne, znane również jako coboty, stanowią przełom w robotyzacji przemysłu dzięki swojej zdolności do bezpośredniej interakcji z ludźmi. W przeciwieństwie do tradycyjnych robotów przemysłowych, które muszą być oddzielone barierami bezpieczeństwa, coboty są zaprojektowane tak, aby bezpiecznie współpracować z ludźmi w tej samej przestrzeni roboczej. Ta cecha sprawia, że są one idealne dla małych i średnich przedsiębiorstw, które potrzebują elastycznych rozwiązań automatyzacyjnych, ale nie mogą sobie pozwolić na całkowitą przebudowę linii produkcyjnych.
Do 2025 roku coboty ewoluowały, zyskując zwiększoną autonomię dzięki integracji zaawansowanego oprogramowania i czujników, które pozwalają im wykonywać bardziej złożone zadania i adaptować się do zmian w czasie rzeczywistym. Łatwość użytkowania to kolejna kluczowa cecha współczesnych cobotów – uproszczone programowanie umożliwia obsługę przez osoby bez specjalistycznej wiedzy technicznej, co zwiększa ich dostępność dla małych i średnich przedsiębiorstw. Ponadto, dzięki rozwojowi technologicznemu i wbudowanym funkcjom bezpieczeństwa, coboty zapewniają bezpieczną interakcję z operatorami ludzkimi nawet w środowiskach wysokiego ryzyka.
Coboty nie zastępują ludzi, ale współpracują z nimi, przejmując monotonne, powtarzalne i nieergonomiczne zadania, dzięki czemu pracownicy mogą skupić się na bardziej kreatywnych i wartościowych aspektach produkcji.
Zastosowania cobotów w różnych branżach
Coboty znajdują zastosowanie w wielu branżach, od produkcji elektroniki po przemysł spożywczy. W montażu elektroniki, coboty mogą wykonywać precyzyjne zadania, takie jak lutowanie komponentów czy montaż drobnych części. W przemyśle motoryzacyjnym, współpracują z ludźmi przy montażu podzespołów, kontroli jakości czy nakładaniu uszczelnień. Elastyczność cobotów sprawia, że mogą być szybko przeprogramowane do wykonywania różnych zadań, co jest szczególnie cenne w produkcji małoseryjnej i spersonalizowanej.
Coboty rewolucjonizują również przemysł spożywczy, gdzie mogą być wykorzystywane do pakowania produktów, sortowania i kontroli jakości. Dzięki zaawansowanym systemom wizyjnym i czujnikom, mogą wykrywać defekty i zapewniać, że tylko produkty spełniające standardy jakości trafiają do konsumentów. W branży farmaceutycznej, coboty wspierają procesy produkcyjne wymagające sterylnych warunków i wysokiej precyzji, minimalizując ryzyko ludzkiego błędu i kontaminacji.
3. Cyfrowe bliźniaki i symulacje w robotyzacji
Cyfrowe bliźniaki to wirtualne reprezentacje fizycznych obiektów, procesów lub systemów, które wykorzystują dane z czujników, symulacje i sztuczną inteligencję do optymalizacji wydajności. W kontekście robotyzacji przemysłu, cyfrowe bliźniaki umożliwiają testowanie i optymalizację procesów produkcyjnych w wirtualnym środowisku przed ich wdrożeniem w rzeczywistości. Ta technologia pozwala na znaczące oszczędności czasu i kosztów, eliminując potrzebę fizycznych prototypów i umożliwiając identyfikację potencjalnych problemów na wczesnym etapie.
W 2025 roku cyfrowe bliźniaki robotów, maszyn, produktów, a nawet całych fabryk wykorzystują symulacje, sztuczną inteligencję i uczenie maszynowe do przewidywania i optymalizacji wydajności pod kątem jakości i efektywności. Dzięki temu możliwe jest testowanie różnych scenariuszy produkcyjnych, optymalizacja ścieżek robotów, identyfikacja wąskich gardeł i przewidywanie potencjalnych awarii – wszystko to w wirtualnym środowisku, bez ryzyka i kosztów związanych z eksperymentowaniem na rzeczywistej linii produkcyjnej.
Korzyści z wykorzystania cyfrowych bliźniaków
Implementacja cyfrowych bliźniaków w robotyzacji przemysłu przynosi liczne korzyści. Przede wszystkim, umożliwiają one optymalizację procesów produkcyjnych poprzez symulację różnych scenariuszy i identyfikację najbardziej efektywnych rozwiązań. Dzięki cyfrowym bliźniakom możliwe jest również predykcyjne utrzymanie ruchu, które pozwala na wykrywanie potencjalnych awarii przed ich wystąpieniem i planowanie konserwacji w najbardziej dogodnym czasie, minimalizując nieplanowane przestoje.
Cyfrowe bliźniaki wspierają także szkolenie operatorów robotów i personelu technicznego. W wirtualnym środowisku pracownicy mogą bezpiecznie uczyć się obsługi skomplikowanych maszyn i systemów, bez ryzyka uszkodzenia sprzętu czy wypadków. Ponadto, cyfrowe bliźniaki ułatwiają współpracę między różnymi działami przedsiębiorstwa, umożliwiając inżynierom, projektantom i operatorom wspólne rozwiązywanie problemów i optymalizację procesów produkcyjnych.
- Testowanie nowych konfiguracji robotów bez przestojów produkcyjnych
- Optymalizacja ścieżek robotów i redukcja czasu cyklu
- Wykrywanie potencjalnych kolizji i problemów bezpieczeństwa
- Szkolenie operatorów w wirtualnym środowisku
- Predykcyjne utrzymanie ruchu i planowanie konserwacji
4. Integracja IoT i robotyki w inteligentnych fabrykach
Internet Rzeczy (IoT) w połączeniu z robotyką tworzy fundament dla inteligentnych fabryk przyszłości. Sieć połączonych urządzeń, czujników i robotów umożliwia zbieranie i analizę ogromnych ilości danych w czasie rzeczywistym, co prowadzi do optymalizacji procesów produkcyjnych i podejmowania lepszych decyzji biznesowych. W 2025 roku inteligentne fabryki wykorzystują zaawansowane technologie IoT do monitorowania stanu maszyn, śledzenia przepływu materiałów i zarządzania energią, co przekłada się na zwiększoną wydajność i obniżenie kosztów operacyjnych.
Przemysłowy Internet Rzeczy (IIoT) umożliwia tworzenie sieci fizycznych urządzeń, pojazdów, budynków i innych obiektów wyposażonych w elektronikę, oprogramowanie, czujniki i łączność sieciową. IIoT pozwala na monitorowanie i zbieranie danych w czasie rzeczywistym z różnych procesów produkcyjnych, co poprawia świadomość sytuacyjną, efektywność operacyjną i umożliwia predykcyjne utrzymanie ruchu w złożonych środowiskach produkcyjnych.
Kluczowe komponenty inteligentnych fabryk
Inteligentne fabryki składają się z wielu zintegrowanych komponentów, które współpracują ze sobą, tworząc spójny ekosystem produkcyjny. Systemy wykonawcze produkcji (MES) monitorują i kontrolują operacje produkcyjne w czasie rzeczywistym, poprawiając wydajność, redukując odpady i zapewniając zgodność ze standardami produkcyjnymi. Integracja MES z urządzeniami IoT zapewnia kompleksowy widok procesu produkcyjnego, umożliwiając identyfikację wąskich gardeł, monitorowanie stanu sprzętu i optymalizację wykorzystania zasobów.
Innym istotnym komponentem są systemy SCADA (Supervisory Control and Data Acquisition), które umożliwiają nadzór i kontrolę procesów przemysłowych. Integracja różnych maszyn i sprzętu, w tym sterowników PLC (Programmable Logic Controllers), maszyn CNC, systemów SCADA, interfejsów HMI (Human Machine Interface) oraz protokołów komunikacyjnych takich jak Modbus, OPC-UA, EtherCAT i PROFINET, zapewnia interoperacyjność i usprawnia procesy produkcyjne. Dodatkowo, technologie RFID, kody kreskowe i kody QR umożliwiają śledzenie produktów w czasie rzeczywistym, co jest kluczowe dla zarządzania łańcuchem dostaw i zapewnienia jakości.
Komponent | Funkcja | Korzyści |
Systemy MES | Monitorowanie i kontrola produkcji | Zwiększenie wydajności, redukcja odpadów |
Systemy SCADA | Nadzór i kontrola procesów | Lepsza kontrola, szybsza reakcja na problemy |
Sterowniki PLC | Automatyzacja procesów | Precyzyjna kontrola, niezawodność |
Technologie RFID | Śledzenie produktów | Lepsza identyfikowalność, zarządzanie zapasami |
5. Predykcyjne utrzymanie ruchu w robotyce przemysłowej
Predykcyjne utrzymanie ruchu to strategia, która wykorzystuje analizę danych, uczenie maszynowe i inne techniki predykcyjne do przewidywania, kiedy sprzęt lub maszyny mogą ulec awarii. Dzięki temu możliwe jest przeprowadzenie konserwacji przed wystąpieniem kosztownej awarii. W kontekście robotyki przemysłowej, predykcyjne utrzymanie ruchu staje się jednym z najszybciej rozwijających się obszarów zastosowania uczenia maszynowego, z prognozowanym wzrostem z 28% firm wykorzystujących tę technologię w 2020 roku do 66% planujących jej wdrożenie do 2025 roku.
W przeciwieństwie do tradycyjnych podejść do konserwacji, które często są reaktywne lub nadmiernie prewencyjne, predykcyjne utrzymanie ruchu koncentruje się na rozwiązywaniu problemów przed ich eskalacją. Historyczne dane z czujników, urządzeń IoT i innych źródeł są analizowane w celu identyfikacji wzorców i trendów, które mogą prowadzić do awarii sprzętu. Monitorując czynniki takie jak temperatura, wibracje, ciśnienie i wzorce użytkowania, algorytmy predykcyjnego utrzymania ruchu mogą przewidzieć potencjalne problemy i zalecić działania konserwacyjne, aby zapobiec przestojom i kosztownym awariom.
Implementacja predykcyjnego utrzymania ruchu
Wdrożenie predykcyjnego utrzymania ruchu w robotyce przemysłowej wymaga odpowiedniej infrastruktury i narzędzi. Kluczowym elementem są czujniki IoT, które zbierają dane o stanie robotów i maszyn w czasie rzeczywistym, monitorując parametry takie jak temperatura silników, wibracje, zużycie energii czy precyzja ruchów. Dane te są następnie analizowane przez zaawansowane algorytmy uczenia maszynowego, które identyfikują anomalie i przewidują potencjalne awarie.
Korzyści z wdrożenia predykcyjnego utrzymania ruchu są znaczące. Obejmują one zmniejszenie nieplanowanych przestojów nawet o 50%, wydłużenie żywotności sprzętu o 20-40%, a także redukcję kosztów konserwacji o 25-30%. Ponadto, predykcyjne utrzymanie ruchu zwiększa bezpieczeństwo pracowników, minimalizując ryzyko wypadków spowodowanych awarią sprzętu.
Predykcyjne utrzymanie ruchu to nie tylko technologia, ale strategia biznesowa, która przekształca podejście do zarządzania zasobami produkcyjnymi, umożliwiając firmom przejście od reaktywnego do proaktywnego modelu operacyjnego.
Podsumowując, robotyzacja przemysłu rozwija się w niezwykle dynamicznym tempie, a pięć omówionych trendów – integracja AI i uczenia maszynowego, rozwój cobotów, wykorzystanie cyfrowych bliźniaków, integracja IoT oraz predykcyjne utrzymanie ruchu – będą kształtować przyszłość produkcji w nadchodzących latach. Firmy, które zdecydują się na wdrożenie tych innowacyjnych rozwiązań, zyskają przewagę konkurencyjną dzięki zwiększonej wydajności, elastyczności i jakości produkcji.
Czy Twoja firma jest gotowa na robotyzację? Jakie wyzwania widzisz w implementacji tych technologii? Podziel się swoimi przemyśleniami i doświadczeniami!
Tekst promocyjny